Imagine a retailer that provides a stellar sales experience that results in a purchase, only for something to go wrong in the process of getting the order to the customer. Any type of error that prevents products from reaching their final destination in a timely manner is aggravating to both customers and the companies that serve them. Organizations also pay in the forms of added costs for returns and reshipping, customer churn, and burdened customer service teams.
What Are Common Shipping Errors?
A majority of customers (90%) and small to midsize businesses (79%) agree that shipping influences at least half of the overall online shopping experience, according to a report by UPS Capital. More than half of buyers say they are apt to leave damaging online reviews to express their dissatisfaction, while separate research finds that more than three-quarters of dissatisfied online shoppers say they’re less likely to buy from a brand again.
Among customers’ biggest shipping-related complaints are late deliveries, lost orders, and damaged products, per UPS Capital. These issues often stem from inefficient operational practices, particularly those that involve manual processes and occurring anywhere in the order lifecycle: order placement, processing, picking and packing, or shipping.
What might go wrong? Here are 10 of the most common reasons for shipping errors.
- Incorrect address: This can be due to something as simple as a typo made by a customer or sales representative when entering an address or neglecting to include an apartment number. In other instances, customers mistakenly designate their billing address as their shipping address when the two, in fact, differ. Failure to cross-reference addresses with an address verification system maintained by postal services and carriers also lets mistakes slip by.
- Wrong item shipped: Order mistakes can start in receiving, when warehouse workers accept incorrect items, improperly label them, or store them in the wrong locations. Manual picking errors during order fulfillment are another culprit, typically the result of the incorrect labeling of products and picking bins. Substitutions made for out-of-stock products—which real-time inventory tracking would have likely caught in the first place—also risk disappointing customers.
- Damaged goods: Failure to optimize packaging for different product types and sizes can stem from substandard packing materials, including outer boxes and inner cushioning. Packaging that is improperly sealed or lacks labeling denoting fragile contents also can cause goods to become damaged en route to the customer—one of the top three pet peeves cited in a survey of online shoppers.
- Late deliveries: Shipments that don’t arrive on timelead the list of delivery issues that cause online shoppers to contact customer service, according to UPS Capital. Reasons for shipping delays abound, ranging fromincorrect shipping data, insufficient postage, or manual order fulfillment to external factors, such as bad weather, a supply chain disruption, or a national holiday.
- Overcharges on shipping: One incorrect ZIP code number can send a shipment much farther than intended, resulting in a higher associated shipping rate that customers must bear or companies must refund. Outsized packaging or overestimating package weight and dimensions when calculating postage also cause overcharges. So does assigning packages to incorrect shipping classes, failing to adhere to carriers’ shipping rules and restrictions, and unfamiliarity with seasonal shipping rates.
- Lost packages: Packages sometimes go missing in transit. Shipping labels that are incorrect, incomplete, or damaged result in packages becoming lost on the way to their destinations. Likewise, incorrect, incomplete, or unverified addresses are common culprits. Carrier sorting errors also lead to packages becoming misplaced.
- Duplicate shipments: Errors in order processing and shipping can result in companies mistakenly sending the same order multiple times. Inventory and order management systems that don’t update in real time can cause glitches, and manual processes are especially error-prone. Additionally, as customer service and fulfillment teams attempt to address delivery delays or rerouting requests, lack of synchronization between the two can manifest in repeat shipments.
- Incorrect shipping method: Whether it’s a customer who mistakenly chooses expedited over standard delivery during the checkout process or an order clerk who selects a slower shipping option than the customer wanted when processing the transaction, a delivery that doesn’t match expectations is never desirable.
- Customs documentation errors: Inaccurate or incomplete documents, such as bills of lading, commercial invoices, and certificates of conformity and country of origin, can cause customs officials to delay shipment clearances, impose fines and storage fees, or reject shipments outright. Incorrect export documentation can also trigger inspections and legal issues when declared information is out of compliance with customs regulations.
- Inventory mismatches: Without an inventory management system that updates in real time, companies risk taking orders for out-of-stock products, leaving customers wondering where their orders are. Manual inventory counts or failure to regularly audit inventory levels pose an even higher likelihood of such stockout-related issues. Inventory mismatches can also be caused by improperly labeled products and picking bins, resulting in the wrong items being selected and shipped.
How to Reduce Shipping Errors: 10 Strategies
Effective strategies to minimize shipping errors prioritize operational efficiencies through automation and technology, standardized practices, employee training, and quality-control measures. Let’s take a closer look at 10 shipping strategies.
- Automate order processing: Manual data entry can introduce mistakes that delay the entire shipping process from receipt of inventory at a warehouse to order fulfillment. Automation streamlines order allocation and increases order accuracy and operational efficiency. It also decreases the likelihood of additional expenses tied to order returns and reshipping. In fact, nearly one-quarter of small to midsize businesses say they spend more than $5,000 per month on damaged, lost, or stolen shipments, which includes the costs of reshipping new items, according to UPS Capital.
- Implement barcode scanning: Barcodes eliminate the need for manual entry of product data when items are first received by a distributor, warehouse, business, or any other entity that will ultimately be shipping goods to end customers. The stock-keeping units (SKUs) of outbound products are scanned with a mobile device at each stage of the fulfillment process to ensure proper selection and overall order integrity. Another benefit: When these devices are integrated with systems that handle inventory, order, and warehouse management, stock levels are automatically updated in real time, improving operational efficiency.
- Use standardized packaging: Standardized packaging and shipping instructions help employees select the packaging and padding materials most befitting product type and dimensional weight. This protects items from damage during shipping and minimizes overcharging for postage.
- Double-check orders: To ensure order accuracy, it’s a good idea to reverify all information associated with the shipment—the products picked, shipping addresses, shipping-level selections, and postage—prior to releasing packages to carriers. Barcode scanning allows for fast confirmation that products and desired quantities match order information to protect against the costs of processing returns and reshipping and foster customer trust.
- Train employees: Ongoing training of fulfillment personnel should include clearly defined shipping procedures, goals, and expectations, as well as employee feedback loops to help address recurring errors and other issues that workers identify. Upskilling after assessing employees’ strengths and weaknesses can improve quality control and cut costs, including costs tied to time spent on customer service to resolve shipping issues.
- Optimize inventory management: Automated inventory management systems using barcode scanning curtail stock mix-ups and misplacements.Strong inventory practices begin with verifying that the correct inbound products are received—items, for example, shipped from a manufacturer to a retailer—and include corresponding item labels. Standardized putaway procedures ensure that products will be stored in their designated areas and in clearly marked picking bins. Real-time inventory tracking systems can pinpoint the locations of each product to maximize picking efficiency and prevent errors.
- Offer real-time tracking: Real-time tracking allows companies and their customers to monitor the whereabouts of their orders and expected delivery times. Features—including live routing maps, delivery exception alerts for unexpected delays, and notification of package delivery to thwart so-called “package pirates”—help both parties proactively address potential concerns. Such transparency also fosters strong relationships with customers, who generally expect resolution of shipping-related issues within two to three business days, according to a global consumer survey.
- Integrate shipping software with carrier systems: Syncing shipping software with multiple carrier systems paves the way for easier and more accurate rate and service comparisons, including transit routes and delivery dates. This integration precludes the manual re-entering of package and destination details, reducing errors. Customers can choose the shipping options that best suit their needs, with access to rates encompassing shipping, insurance, and other carrier fees. The software usually includes address verification tools, the ability to purchase labels, and real-time tracking and delivery confirmations.
- Maintain clear labeling: Legible address details are essential if shipments are to arrive where they’re intended to go. Automated address validation systems that standardize address formats and verify them against postal service and carrier databases ensure accuracy and reduce potential added costs stemming from address correction surcharges. Some systems also integrate directly with label-printing processes.
- Analyze shipping data: Businesses with integrated inventory, order, and warehouse management systems that collect and analyze volumes of real-time shipping data can quickly identify (and remedy) bottlenecks in the shipping process or other inefficiencies that result in recurring errors. Those systems can also detect sales trends, optimize shipping routes, and monitor order fulfillment key performance indicators, such as on-time delivery rates, to improve shipping accuracy and efficiency.
Reduce Shipping Errors With NetSuite
Whether due to a mistyped address, a mislabeled product, or poor packaging, any error that prevents the right products from reaching customers on time and in pristine condition can cut into an organization’s revenue and profitability. NetSuite Warehouse Management System (WMS) helps prevent a multitude of costly mistakes from being made during product receiving, storage, and order fulfillment by replacing error-prone manual processes with automated workflows. These workflows optimize putaway and pick-and-pack processes, as well as warehouse task management and returned merchandise authorizations.
In addition, the cloud-based WMS includes best-in-class features, such as mobile radio-frequency barcode scanning to ensure accurate product identification and placement and automated cycle counting to confirm that physical inventory matches inventory records. Integration with parcel and freight carrier shipping systems validates addresses, compares shipping rates, and generates accurate labels. These capabilities, among others, help businesses reduce shipping errors, lower fulfillment costs, and maintain customer satisfaction.
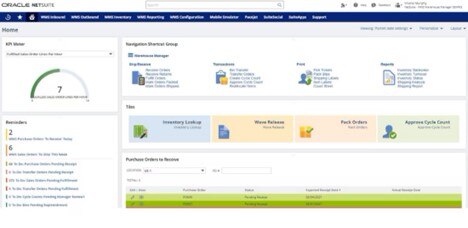
Shipping errors can undermine even the strongest customer experience. The consequences extend beyond immediate financial impacts, such as covering the costs of returns and reshipments; customer trust and loyalty are also at risk. But with automated technology, standardized processes, and proper employee training, businesses can avoid many of the common shipping errors that occur during receiving, order processing, picking, packing, and delivery. Real-time inventory tracking, barcode scanning, and integrated shipping software create multiple checkpoints throughout the fulfillment process, resulting in the right products reaching the right customers at the right time.
#1 Cloud ERP
Software
Prevent Shipping Errors FAQs
How do you reduce inaccurate order deliveries?
Software that automates inventory, order, and warehouse processes mitigates the chances of incorrect order deliveries by eliminating human errors associated with manual data entry and fulfillment processes. Automation handles inventory counts, address verification, and other areas where accuracy is key.
How can I make shipping more efficient?
Automation technology streamlines shipping with optimized product picking and standardized packaging that protects products from damage. Integrations with parcel and freight carrier systems set the stage for cost-effective shipping with proper address information and postage.
What is an acceptable shipping error rate?
When it comes to potential lost revenue and customer alienation, there is no acceptable shipping error rate. Shipping mistakes impact the bottom lines of companies forced to cover the added expenses of returns, order reshipments, and time spent by customer service and fulfillment employees resolving the logistical issues. Frustrated customers, meanwhile, could think twice when placing new orders and turn instead to competing businesses.