Material requirements planning (MRP) is a standard supply planning system to help businesses, primarily product-based manufacturers, understand inventory requirements while balancing supply and demand. Businesses use MRP systems, which are subsets of supply chain management systems, to efficiently manage inventory, schedule production, and deliver the right product—on time and at optimal cost.
What is Material Requirements Planning (MRP)?
MRP software is a management tool that manufacturers use to better control their inventory by determining what materials they need, in what quantities, and when they need them for production. To make this determination, MRP software combines data from procurement and production systems, including current inventory levels, open purchase orders, expected sales, and assembly schedules.
The software’s analytics features then use this data to suggest strategies that allow businesses to align inventory levels with forecasted demand without creating stock deficits or surpluses. Procurement teams that adopt this data-driven strategy are then able to time purchase orders in a way that reduces costs and declutters shelves without negatively impacting the customer experience.
Dependent vs. Independent Demand
Planning material needs effectively requires manufacturers to manage two types of demand: independent and dependent. Independent demand comes from external sources, such as customer orders or market trends, and companies typically rely on forecasting tools to predict the direct sales driven by this kind of demand. Dependent demand, on the other hand, is calculated based on the components or subassemblies that make up the pieces of those expected sales. For example, if a furniture manufacturer sells four-legged tables, demand for the tables is independent, but leg production will depend entirely on table sales, as each table requires the company to manufacture four legs (among other components). MRP systems monitor the relationship between finished goods and their components to precisely calculate material requirements and plan production schedules based on this expected demand.
Key Takeaways
- Manufacturers use MRP systems to calculate what materials they’ll need, in what quantities, and when materials should arrive to meet production needs.
- MRP systems integrate data from several sources—demand, bills of materials, inventory, and master production schedules—to predict material requirements.
- This information is then used to optimize inventory levels and production schedules.
- The primary objective of MRP is to maintain enough inventory to avoid stockouts and overstocks without raising costs or sacrificing product quality and delivery times.
Video: MRP Defined
MRP Explained
MRP software automates critical manufacturing steps to speed up and enhance material processes, including procurement and storage operations. First, it analyzes sales orders and demand forecasts to determine production expectations. Then, it uses documents that list each product’s required components, known as bills of materials (BOMs), to calculate precise quantities for each production run. Over time, the system continuously updates material requirements and adjusts supply orders and inventory levels as demand changes. This automation helps manufacturers avoid common issues, such as production delays from material shortages, excess inventory draining resources, and rushed orders to compensate for poor planning. Proactive material management allows businesses to eliminate error-prone manual steps and high shipping costs for expedited or emergency supply runs, ultimately giving customers more reliable quality and delivery expectations at a lower cost for the company.
How MRP Works
An MRP system accelerates the manufacturing production process by determining what raw materials, components, and subassemblies are needed, and when to assemble the finished goods, based on demand and BOMs. It does this by asking three main questions:
- What is needed?
- How much is needed?
- When is it needed?
The answers to these questions provide clarity into what materials are needed, how many, and when to fulfill the required demand and help facilitate an efficient and effective production schedule.
Why Is MRP Important?
MRP gives businesses visibility into the inventory requirements needed to meet demand, helping your business optimize inventory levels and production schedules. Without this insight, companies have limited visibility and responsiveness, which can lead to:
- Ordering too much inventory, which increases carrying costs and ties up more cash in inventory overhead that could be used elsewhere.
- Inability to meet demand because of insufficient raw materials, resulting in lost sales, canceled contracts, and out-of-stocks.
- Disruptions in the production cycle, delaying subassembly builds that result in increased production costs and decreased output.
MRP in Manufacturing
Because MRP systems originated in the manufacturing sector, it’s appropriate that manufacturers are the primary users. These systems are particularly valuable for companies that produce complex goods that depend on multiple components and assembly processes, such as automotive, electronics, and industrial equipment. But even relatively simple manufacturing operations can leverage MRP systems to adopt leaner principles and minimize material stockouts or overstock without slowing down production. For example, if a manufacturer receives a large custom order, its MRP system can automatically calculate all required components, from raw materials to subassemblies, and place purchase orders as needed. This way, the business can meet the delivery deadline without using up entire inventory reserves meant for day-to-day output.
What Other Industries Use MRP?
Outside of manufacturing, various industries have adopted MRP to better manage inventory and balance supply and demand. However, unlike dedicated MRP systems, these adaptations usually focus more on managing the finished goods that comprise a business’s core operations, rather than the component-level planning central to manufacturing. Here are some common examples.
- Healthcare facilities apply MRP to manage medical supplies and pharmaceutical inventory, especially during seasonal spikes in care requirements, such as flu season.
- Distribution companies use MRP tools to match incoming shipments and orders with expected customer demand, minimizing dead stock for out-of-date goods.
- Restaurants use MRP systems to track and replenish ingredients and minimize spoilage during periods of changing customer preferences and prices due to seasonal shifts or supply chain slowdowns.
- Service industries, such as maintenance and repair operations, incorporate MRP tools into their systems to help guarantee that they have the right parts and supplies available for scheduled maintenance work.
MRP Steps and Processes
The MRP process can be broken down into four major steps.
1. Identifying Requirements to Meet Demand
The first step of the MRP process is identifying customer demand and the requirements needed to meet it, which starts with inputting customer orders and sales forecasts.
Using the BOM required for production, MRP then disassembles demand into the individual components and raw materials needed to complete the build while accounting for any required subassemblies.
2. Checking Inventory and Allocating Resources
Utilizing MRP to check demand against inventory and allocating resources accordingly, you can see both what items you have in stock and where they are—this is especially important if you have inventory across several locations or inventory discrepancies. This also lets you see the status of items, which gives visibility into items that are already allocated to another build, as well as items not yet physically in the warehouse that are in transit or on order. The MRP then moves inventory into the proper locations and prompts reorder recommendations.
3. Scheduling Production
Using the master production schedule, the system determines how much time and labor are required to complete each step of each build and when they need to happen so that the production can occur without delay.
The production schedule also identifies what machinery and workstations are needed for each step and generates the appropriate work orders, purchase orders, and transfer orders. If the build requires subassemblies, the system takes into account how much time each subassembly takes and schedules them accordingly.
4. Identifying Issues and Making Recommendations
Finally, because the MRP links raw materials to work orders and customer orders, it can automatically alert your team when items are delayed and make recommendations for existing orders: automatically moving production in or out, performing what-if analyses, and generating exception plans to complete the required builds.
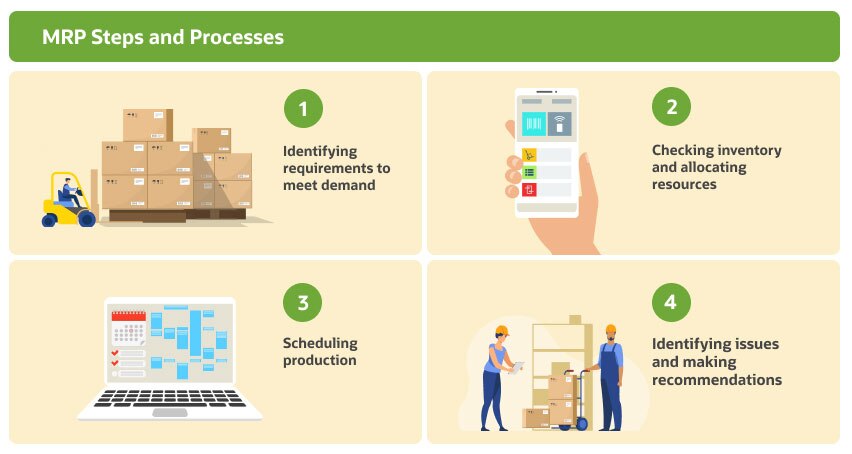
MRP Inputs
How well your MRP system works depends on the quality of the data you provide it. For an MRP system to work efficiently, each input must be accurate and updated. Here are some of the inputs an MRP depends on.
Demand
Demand includes sales forecasts and customer orders. When working with predicted demand, a system that is integrated with a companywide enterprise resource planning (ERP) system allows forecasting using historical sales vs. just sales forecasts.
Bill of Materials
Keeping a single updated version of the BOM is essential for accurate supply forecasting and planning. A system that’s integrated into the enterprisewide inventory management system avoids version control issues and building against outdated bills, which results in reworks and increased waste.
Inventory
It’s essential to have a real-time view of inventory across the organization to understand what items you have on hand and which are en route or have purchase orders issued, where that inventory is, and what the inventory’s status is.
Master Production Schedule
The master production schedule takes all build requirements and plans machinery usage, labor, and workstations to account for all outstanding work orders to be completed.
MRP Outputs
Using the provided inputs, the MRP calculates what materials are needed, how much is needed to complete the build, and when in the build process they are needed.
With this information defined, businesses can execute on just-in-time (JIT) production, scheduling production based on material availability. This minimizes inventory levels and carrying costs, as inventory is not stored in the warehouse for future production but arrives as needed. By scheduling materials to arrive and production to begin soon after, businesses can move materials through the workflow process without delay.
The MRP lays out the plan of when materials should arrive, based on when they’re needed in the production process, and when subassemblies should be scheduled. Using a master production plan and taking into account subassembly build times minimizes materials sitting on shelves and bottlenecks in the build process.
Benefits of MRP
Implementing an MRP system can significantly improve how manufacturers manage their production lines and inventory control. This is especially true when MRP features are built into a larger manufacturing ERP solution, where benefits can echo companywide. The primary benefits of MRP systems include:
- Increased efficiency: MRP systems automate material movements, from original work orders through each assembly step, to make sure the company fulfills customer orders on time and up to quality standards. By eliminating manual processes, such as pulling historical data to forecast sales, teams can instead focus on more productive and complex tasks, such as assisting customers or identifying issues and developing targeted solutions to enhance existing workflows.
- Optimized inventory management: MRP software calculates precise material requirements, and times orders accordingly, supporting businesses as they seek to maintain optimal inventory levels for both raw materials and work-in-progress goods. This comprehensive approach to managing materials allows manufacturers to maintain production speeds without tying up working capital with excess inventory.
- Cost savings: Proactive inventory planning reduces storage costs and minimizes emergency supply orders to replenish empty reserves. When MRP tools are integrated across production lines, businesses can also reduce labor costs associated with manual inventory management, such as moving materials from one warehouse to another when stock is poorly allocated.
- Improved customer satisfaction: MRP software helps manufacturers provide consistent service and build strong customer relationships by preventing production delays and late deliveries. Furthermore, prioritizing material planning and handling makes sure production teams have all the materials they need, in the right quantities, to consistently produce high quality goods and create a more reliable customer experience.
MRP Challenges
Although using an MRP solution is far better than using spreadsheets for supply planning, it’s only as good as its data inputs. The better a business understands and documents its processes, the better the system can serve them. Here are some common challenges to consider when planning and managing an MRP system.
- Data accuracy: MRP systems require precise inventory counts, current BOMs, and accurate lead times to generate accurate outputs. Through regular audits, automated data collection, and systematic review processes, businesses can maintain data integrity and prevent or catch errors before they impact MRP processes.
- System integration: Poorly connected systems can lead to redundancy, corrupt or incomplete information, and siloed data sets—all of which create inconsistencies and misguided decisions. Businesses should fully integrate MRP tools with existing systems, such as ERP solutions, and run validation checks to unlock seamless data flow across the company.
- User training: Learning new systems can frustrate staff, especially when they feel unprepared for the big changes a technology overhaul can bring. Initial and ongoing training, as well as detailed system documentation and phased implementation, help staff understand both the software and its manufacturing processes well enough to properly use the MRP tool’s capabilities and maximize their productivity.
- Process documentation: MRP systems require clear workflow documentation to reflect realistic production capabilities and constraints, and not all manufacturers have a complete set of up-to-date and detailed records on hand. Regular process mapping and updates to standard operating procedures align system settings and expectations with real-world limitations and results.
MRP vs. ERP: What’s the Difference?
Although MRP and ERP systems typically share common features, they serve distinct purposes in modern business operations. MRP systems focus specifically on production planning and inventory control, while ERP systems take a broader approach to business management, often including MRP functionality as part of a larger module suite. ERP systems extend beyond production, integrating all aspects of business operations into one platform, including financial management, customer relationship management, human resources, and supply chain management. When integrated effectively, MRP functions work within the ERP framework to connect information between production planning and other departments. Businesses can leverage this end-to-end visibility to more effectively manage companywide resources and gain a valuable look at how material planning decisions directly and indirectly affect other business areas, such as cash flow or customer satisfaction.
NetSuite’s All-in-One ERP Solution for Manufacturers
NetSuite MRP software leverages advanced demand forecasting and real-time inventory tracking to help manufacturers ensure that materials are available when and where they're needed, reducing the risk of stockouts and overstock. The system’s automated tools accelerate manufacturing by quickly generating work and purchase orders based on detailed inventory data, BOMs, and demand forecasts. And because NetSuite MRP functionality is built directly into its broader ERP system, manufacturers gain complete visibility into how material planning decisions affect everything from cash flow to customer satisfaction. This comprehensive approach helps growing businesses overcome common material planning challenges while building more efficient, profitable operations.
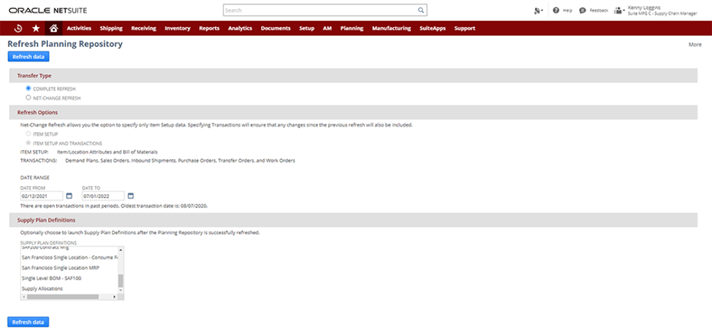
MRP systems have evolved beyond basic inventory management tools into sophisticated digital solutions that give manufacturers a deeper understanding of their entire production process. Through automated material calculations and real-time inventory visibility, MRP systems allow businesses to reduce costs and excess stock at every step of their operation, without impacting their ability to satisfy customer demand. As manufacturers grow and rely on increasingly complex operations and supply chains, prioritizing material planning helps guarantee that production teams will always have the right materials, in the right quantities, exactly when they need them.
#1 Cloud ERP
for Manufacturing
Manufacturing Requirements Planning FAQs
What are the three primary outputs of MRP?
The three primary outputs of material requirements planning (MRP) are materials needed, their optimal quantities, and when they’ll be needed during production. With this information, procurement teams can time orders to minimize stockouts and overstock, and production teams can maintain the inventory levels they need to meet demand.
What are the differences between master planning and MRP?
Master planning focuses on high-level production needs, such as overall sales expectations and long-term manufacturing goals, whereas material requirements planning (MRP) handles the specific material requirements needed to execute that master plan successfully. Put simply, master planning determines what and how much to produce, while MRP determines how much material to order and where and when they’ll be used to fulfill that mission.
What’s the difference between MRP and JIT?
Material requirements planning (MRP) is software that manages material requirements, while just-in-time (JIT) is a manufacturing strategy that aims to minimize inventory by receiving materials at the moment they’re needed for production. While both approaches aim to optimize inventory processes and costs, MRP focuses on proactive planning and scheduling based on sales forecasts, whereas JIT emphasizes the actual flow of materials and is more closely tied with actual demand.
What are the inputs for MRP?
The essential inputs for material requirements planning (MRP) include:
- Demand includes customer orders and sales forecasts, which are based on historical demand.
- Bills of materials list every component of a product, creating an accurate and up-to-date list of all materials needed.
- Inventory data allows procurement teams to see which materials need to be reordered and when to replenish existing stock as it’s used.
- Master production schedules outline planned production quantities, labor and workstation needs, and timing to reach production goals.